Roots Reset in-depot - The biological solution to the Japanese Knotweed problem in construction projects
“Buyers pull out of new-build project due to presence of Japanese knotweed “ and ”Exotic weed plant threatens building sites ’ - headlines like these are becoming increasingly common. Japanese knotweed (often abbreviated as JK), a green menace that not only threatens nature, but can also significantly delay projects and drive up costs. In this post, we dive into the current problem, the time constraints in construction projects and offer a sustainable solution to the Japanese knotweed problem inside and outside construction projects - Roots Reset in-depot.
The rise of Japanese knotweed
Japanese knotweed is like an unwelcome guest that is increasingly popping up in construction projects. Its aggressive growth habit and deep roots make it a nightmare for property developers and construction companies. The timely and effective control of this plant is crucial to avoid delays and extra costs.
Time pressure in the construction industry
Time is precious in the construction industry, where tight deadlines are the norm. Traditional methods of tackling Japanese knotweed, such as excavation and removal of soil infested with Japanese knotweed, are not only costly but can also cause significant delays.
Sustainable alternatives and cost considerations
Several alternatives present themselves, but mostly bring their own challenges and costs. Transporting contaminated soil to external locations such as a thermal cleaner, for example, not only results in high transport costs, but also increases the risk of further spread of Japanese knotweed. Not to mention the high landfill costs of soil contaminated with Japanese knotweed.
Roots Reset in-depot: the sustainable and cost-efficient alternative
This is why we introduce to you the solution to the Japanese knotweed problem in construction - Roots Reset in-depot. This revolutionary method offers property developers and construction companies a sustainable and cost-efficient approach to completely free land from Japanese knotweed and ensure the progress of construction projects.
On-site treatment
Where possible, Roots Reset in-depot can be applied ‘on-site’ at the (construction) site. This dramatically minimises transport costs as the soil is treated in-depot on-site. Where there is space on the construction site to create a depot, this variant of Roots Reset is preferred. This keeps the soil on site, eliminating further spread of the JDK. After treatment, you retain and reuse the clean soil within the project, making it a win-win situation.
Roots Reset in-depot
In situations where on-site treatment is not feasible due to lack of space, the normal Roots Reset in-depot variant offers a solution. The contaminated soil is excavated and transported to a soil depot/soil bank. This method is more cost-effective than traditional disposal methods, such as excavation and transport to a processor, without compromising on sustainability.
Conclusion
Roots Reset in-depot is not just another solution; it is the sustainable key to efficiently addressing the Japanese thousand-node problem within your projects. Save costs, reduce time pressure and preserve clean soil. Choose the future of your (construction) projects, choose Roots Reset in-depot.
The rise of Japanese knotweed
Japanese knotweed is like an unwelcome guest that is increasingly popping up in construction projects. Its aggressive growth habit and deep roots make it a nightmare for property developers and construction companies. The timely and effective control of this plant is crucial to avoid delays and extra costs.
Time pressure in the construction industry
Time is precious in the construction industry, where tight deadlines are the norm. Traditional methods of tackling Japanese knotweed, such as excavation and removal of soil infested with Japanese knotweed, are not only costly but can also cause significant delays.
Sustainable alternatives and cost considerations
Several alternatives present themselves, but mostly bring their own challenges and costs. Transporting contaminated soil to external locations such as a thermal cleaner, for example, not only results in high transport costs, but also increases the risk of further spread of Japanese knotweed. Not to mention the high landfill costs of soil contaminated with Japanese knotweed.
Roots Reset in-depot: the sustainable and cost-efficient alternative
This is why we introduce to you the solution to the Japanese knotweed problem in construction - Roots Reset in-depot. This revolutionary method offers property developers and construction companies a sustainable and cost-efficient approach to completely free land from Japanese knotweed and ensure the progress of construction projects.
On-site treatment
Where possible, Roots Reset in-depot can be applied ‘on-site’ at the (construction) site. This dramatically minimises transport costs as the soil is treated in-depot on-site. Where there is space on the construction site to create a depot, this variant of Roots Reset is preferred. This keeps the soil on site, eliminating further spread of the JDK. After treatment, you retain and reuse the clean soil within the project, making it a win-win situation.
Roots Reset in-depot
In situations where on-site treatment is not feasible due to lack of space, the normal Roots Reset in-depot variant offers a solution. The contaminated soil is excavated and transported to a soil depot/soil bank. This method is more cost-effective than traditional disposal methods, such as excavation and transport to a processor, without compromising on sustainability.
Conclusion
Roots Reset in-depot is not just another solution; it is the sustainable key to efficiently addressing the Japanese thousand-node problem within your projects. Save costs, reduce time pressure and preserve clean soil. Choose the future of your (construction) projects, choose Roots Reset in-depot.
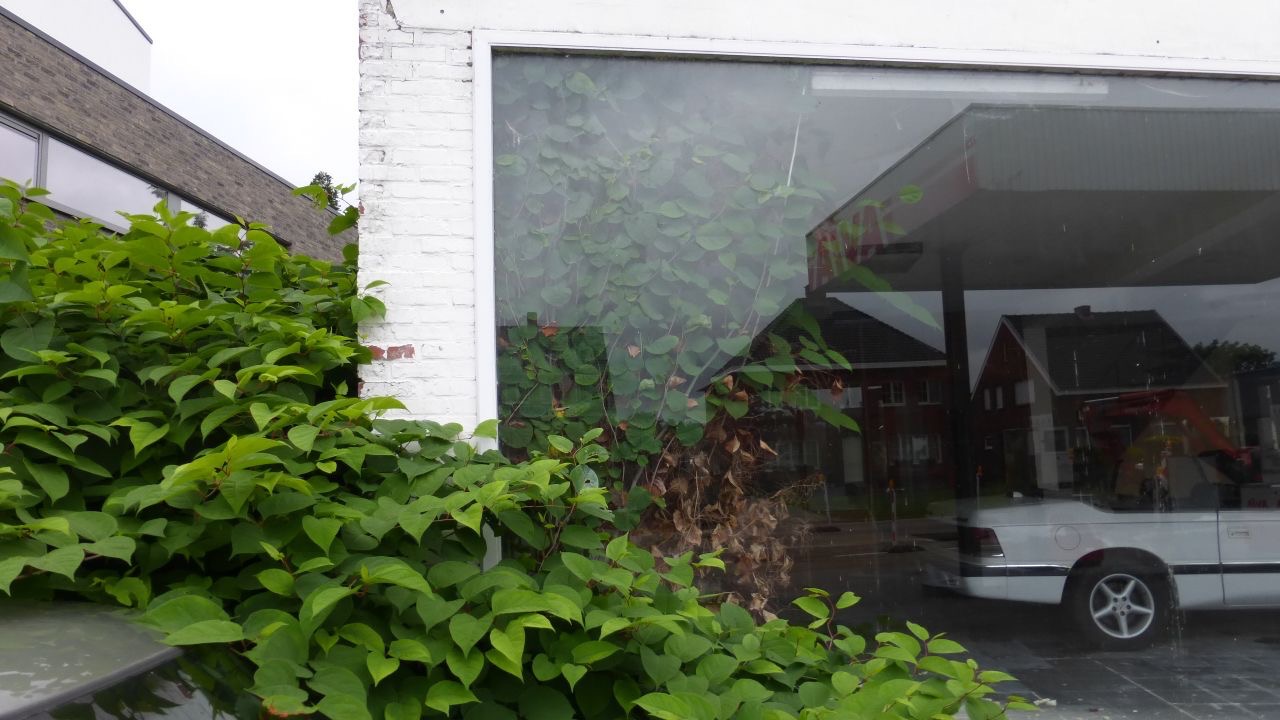
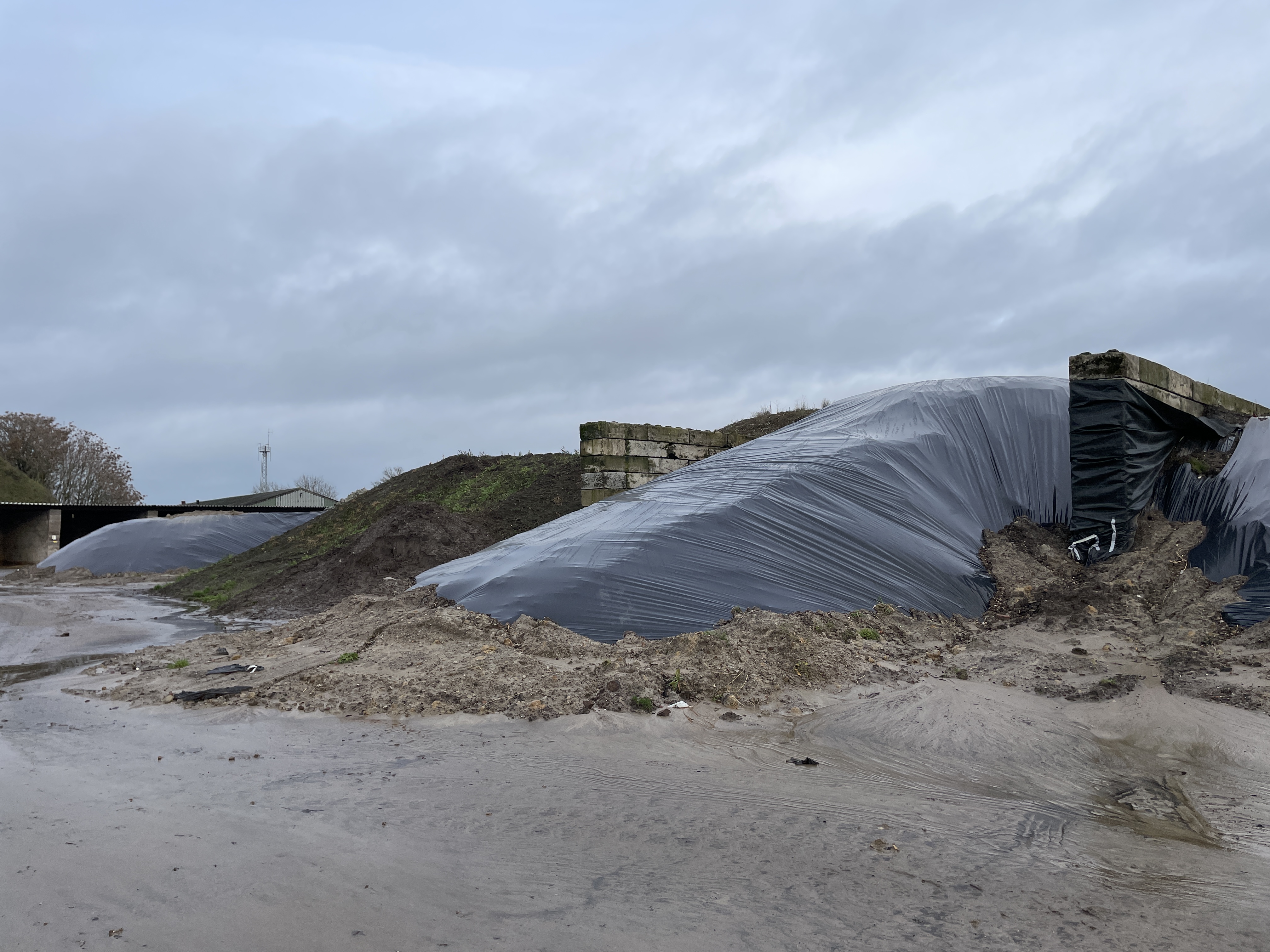
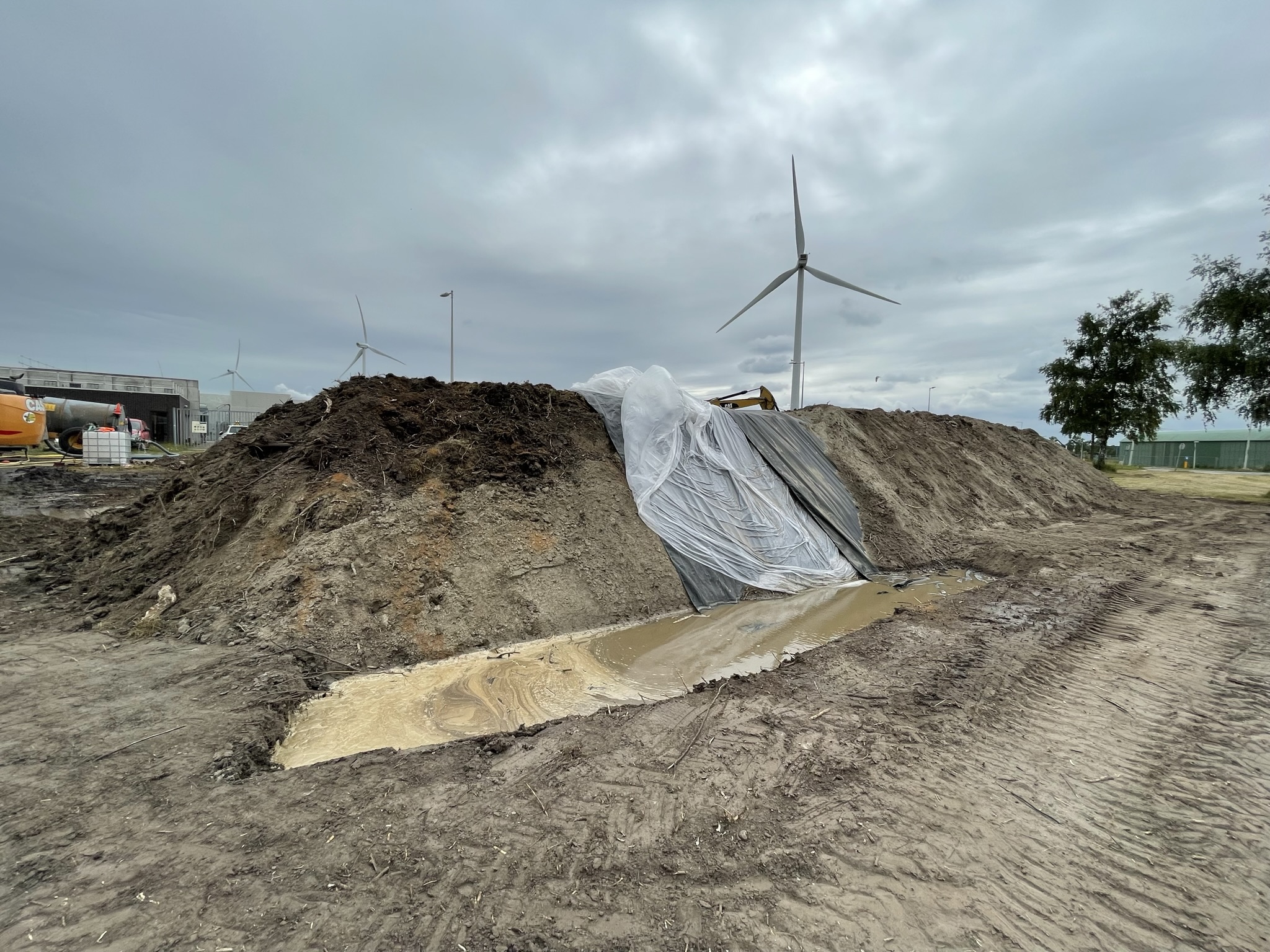
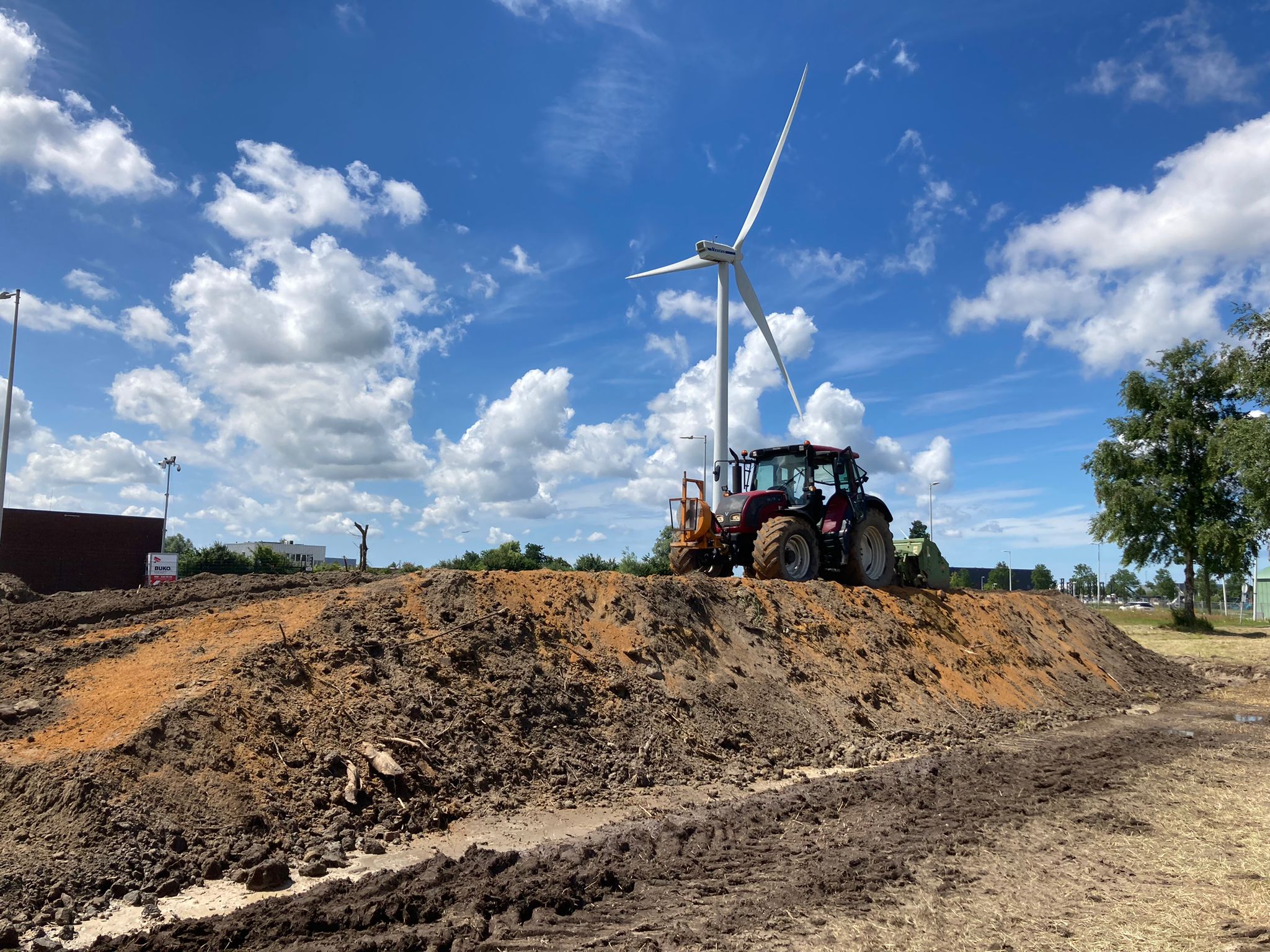
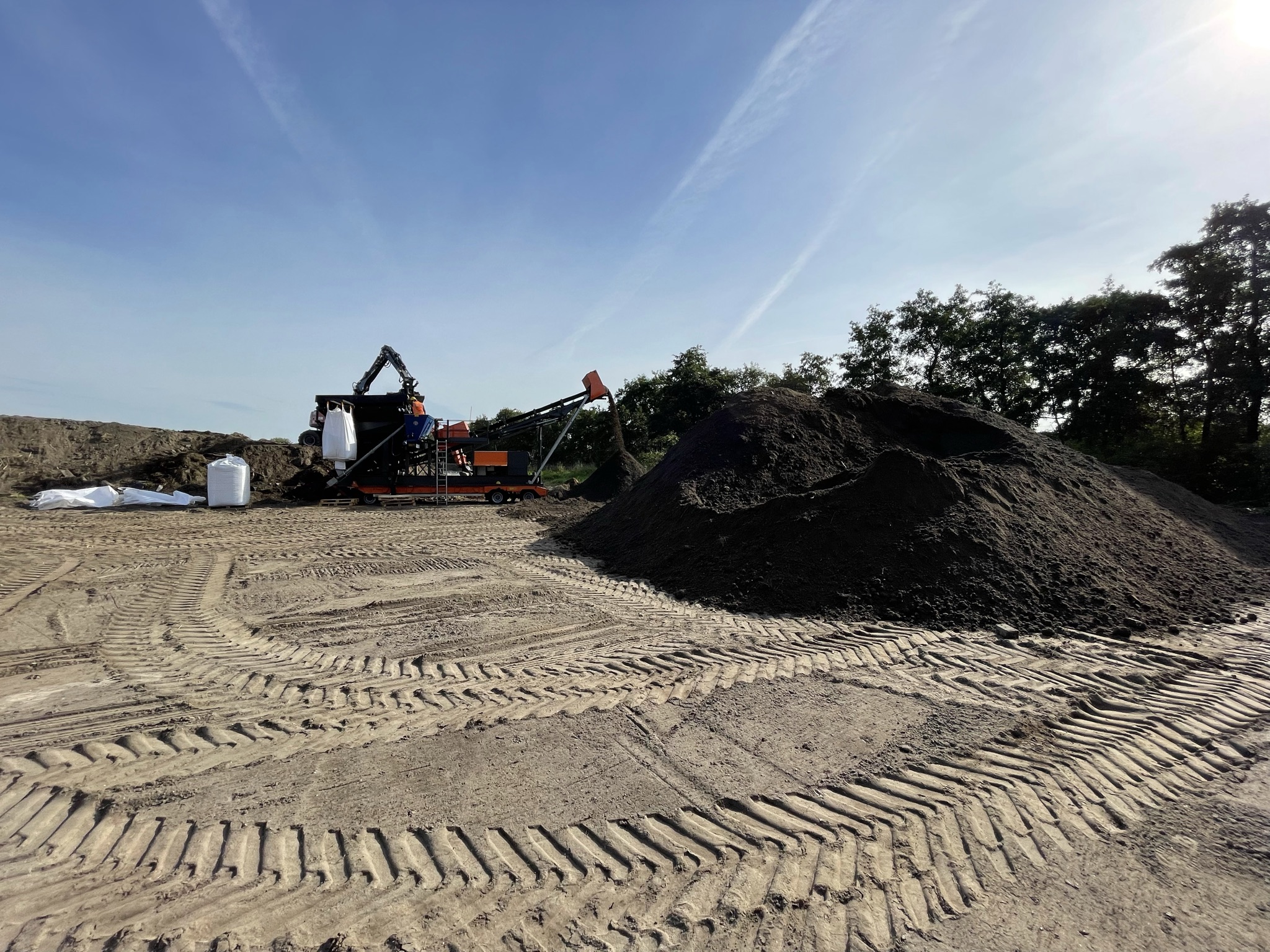